純電動汽車 (BEV) 有嚴重的重量問題,這種問題 Weight Watchers® 無法解決。
許多純電動汽車比內燃機汽車 (ICE) 重 33%。美國國家運輸安全委員會主席指出:「福特 F-150 Lightning比非電動版本重 2000 到 3000 磅。」另外,美國國家經濟研究局 (National Bureau of Economic Research) 發現,車輛每增加 1,000 磅,事故死亡風險就會增加約 47%。
因此,汽車 OEM 廠商在嘗試設計續航里程更長、安全性更高和電子內容更多的純電動汽車時,面臨嚴峻的限制條件。這是該產業有史以來面臨的最嚴峻研發挑戰之一。
儘管面臨巨大的挑戰,但如果電動汽車中的傳統超重供電網路 (PDN) 被 48V 區域架構(zonal architecture)取代,其中 48V 母線取代原有 12V 系統,則可減少 OEM 廠商、消費者和立法者的這些擔憂。部署由高密度電源模組支援的區域架構,將以 3 種方式減輕重量。這種新架構將實現從粗線束到細線束的過渡,可將線束重量減少 85%。此外,低壓輔助電池可拆除並使用電源模組進行虛擬化,從而可完全消除電池重量。最後,使用電源模組進行 PDN 升級,可最佳化熱管理系統,從而將其重量減少 33%。
因此,採用分散式架構替代傳統集中式架構,可顯著減輕重量,還可提高整體電力系統效率。
採用 48V:對於純電動汽車而言,是一項期盼已久的明顯改進 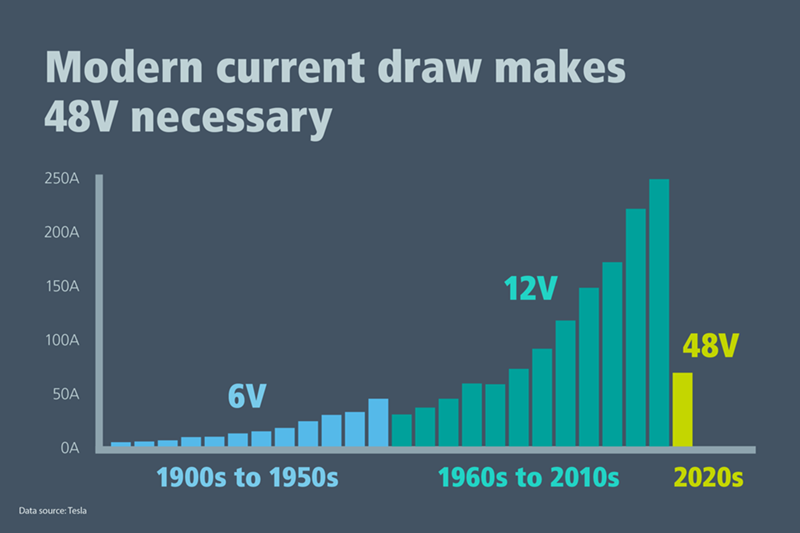 圖1:轉換為 48V 系統,會將車輛總電流從 250A 以上降至 75A 以下,不會影響車輛電氣效能。自 1908 年以來,隨著汽車電子設備的增加,汽車電流需求已呈指數級成長。20 世紀 60 年代,OEM 廠商將電壓從 6V 提高到 12V,導致電流在 60 年首次減少。儘管現在需要更大的電流,但大多數 OEM 廠商仍然使用 12V 母線。2023 年,特斯拉成為首家宣佈在整個汽車中全面採用 48V 母線的 OEM 廠商,這將大大降低電流需求。
在每個設計週期,新車都會增加安全、保全和自動駕駛等新電子產品。每個額外的功能都會增加功耗,使用固定標準化電池已轉化為電流的指數級成長。從電流趨勢來看(圖 1),集中式架構 PDN 是不可持續的。要恢復可持續電流位準並最大限度減少線束重量的同時,滿足不斷成長的電力需求,唯一的方法就是使用區域架構將工作電壓提高至 48V。
目前的純電動汽車由主高壓電池(通常為 400V 或 800V)供電,不僅需要為電動牽引馬達供電,而且還需要為大量低壓負載供電,如空調、加熱座椅和資訊娛樂系統等。PDN 會將高壓降至 48V 及 12V 輔助電池電壓,為這些子系統供電。
根據歐姆定律,轉而採用 48V 分散式架構將帶來一個機會: 功率=電流×電壓。功率輸出相同時,12V 電源需要的電流是 48V 電源的四倍。因此,12V 導線一般也比 48V 導線粗四倍。 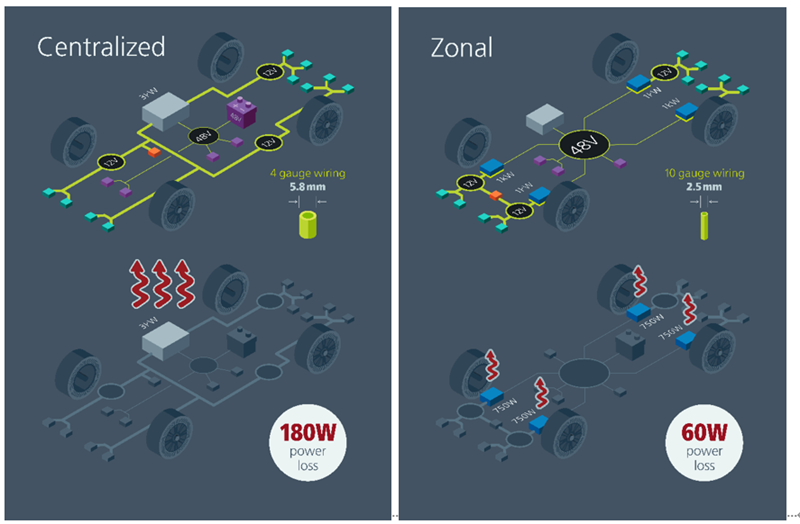 圖2:當今汽車有兩種不同的 PDN:12V 集中式架構和快速發展的 48V 分散式架構。前者採用 12V 粗線束,後者採用 48V 細線束,細線束重量更輕,減少了熱損耗,而且將電流降至 1/4。
終結12V 集中式架構 自 20 世紀 60 年代以來,12V 集中式系統一直是汽車使用的傳統電源架構。該架構由一個龐大的銀盒外殼組成,其中包含一系列分立式元件,例如所有將高壓 (HV) 轉換成 48V 至 12V 的 DC-DC 轉換器等。這個系統需要使用粗重的導線將 12V 電流傳輸至負載點。此外,由於傳統的 DC-DC 轉換效率低,這種集中式電源系統會從銀盒產生大量熱量,通常需要密集的液冷,這會增加更多的重量。
要過渡到 48V,可在端點位置使用高密度電源模組,以便在負載點高效轉換為 12V。這使 OEM 廠商能夠隨著時間的推移,高度靈活地逐漸將 12V 負載器件過渡到 48V。這有助於在對系統架構干擾最小的情況下,快速實現使用 48V 的優勢。
48V 分散式架構降低熱損耗、減少電流
這種新穎的 48V 分散式架構系統利用了歐姆定律,是產業轉變的典範,其中 DC-DC 轉換發生在更靠近負載點的位置,而不是在中央銀盒(Silver Box)內完成。在該方案中,高壓至 48V 的轉換有助於將安全的 48V 用作整個車輛的母線電壓。48V 至 12V 的轉換在負載點位置進行。透過 48V 而非 12V 傳輸電流,導線可以更細、更輕,很明顯,成本也會更低(圖 2)。這種更細、更靈活的導線也更容易在車內佈局。此外,這種方法可將與 DC-DC 轉換器有關的熱損耗均勻地分佈在整個車上,從而可使用安裝在底盤上的熱傳導及空氣對流散熱系統的潛能。
檢視減少的重量 48V 分散式架構不僅可更加支援純電動汽車日益成長的動力需求,同時還可採用 3 種方法減輕汽車重量
1.線束:重量銳減約85%:升級到48V分區架構,意味著傳統的273克/公尺的12V、4號電線將被 27克/公尺的48V、10號電線取代。這可減輕大約85%的導線重量。 2.輔助蓄電池取消:重量減少~100%
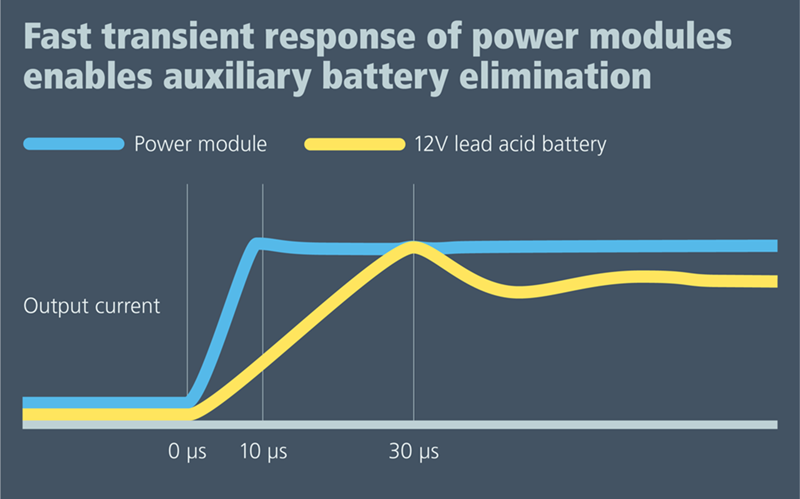 圖 3:電源模組可實現比 12V 鉛酸電池更快的暫態響應,從而建立虛擬電池,可取代傳統的笨重 12V 電池
電源模組的分散式架構可加速 DC-DC 轉換器的暫態響應,從而建立虛擬電池。因此,12V/48V 分散式電源模組不僅可複製 12/48V 低壓電池的特徵,同時完全消除了實體 12V 電池,減輕了 100%的重量。
3.電源系統最佳化:重量減輕約 33% 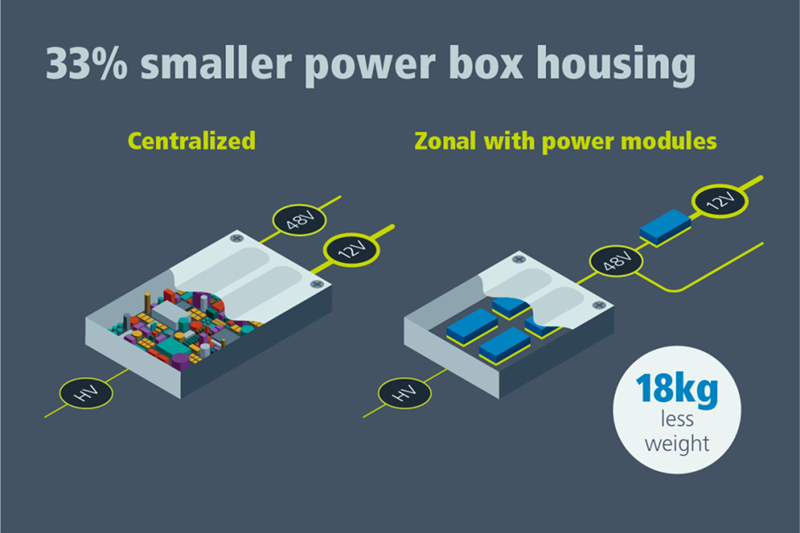 圖 4:使用電源模組和分散式架構時,可縮小集中式外殼,因為在 48V 轉換為 12V 負載的端點可以更有效率地散熱。
用區域系統取代集中式系統,可將 48V 至 12V 電源轉換從銀盒移至負載點。改進後採用高密度電源模組提供 48V 輸出的電源系統盒將縮小達 33%。因此,外殼重量可減輕多達三分之一 (33%)。
在傳統 12V 集中式系統中,分立式元件會在其銀盒外殼內產生環境高溫。採用高密度電源模組的電源系統盒產生的熱量較少,而且負載點模組可在底盤上進行高效的通風散熱。這些改進可使液冷系統瘦身 7%。
化重量為機遇 OEM 廠商可使用分散式架構獲得各種優勢。為了說明這一點,請考慮減輕重量對增加行駛里程的影響。
車輛越重,能耗就越大,行駛里程也就越短。然而,如果將其用來增加電池尺寸,額外的重量就可降低對續航里程的影響。額外的電池提供更多的能量儲存,可增加續航里程。
在 Vicor 進行的一項研究中,高密度電源模組支援的分佈架構可將車輛重量減輕 40 磅(表 1)。在該重量被 40 磅的電池所取代時,在不增加淨重的情況下,電動汽車的行駛里程每年可增加 4000 英里。 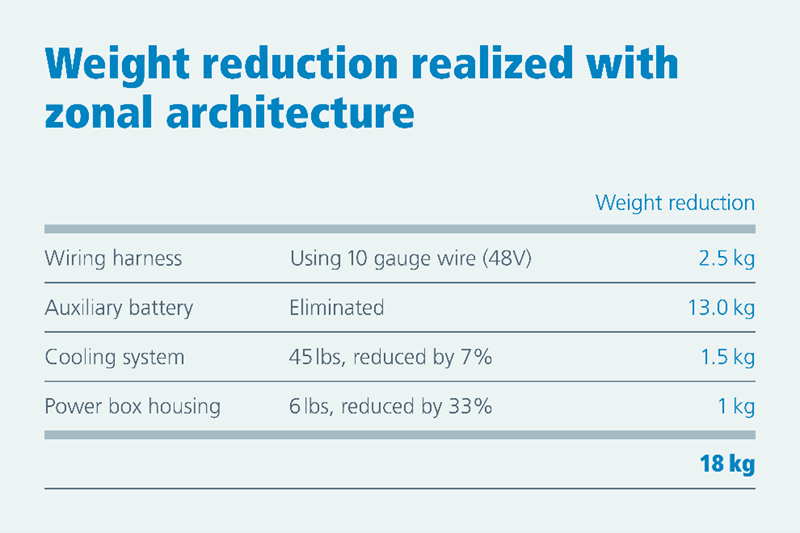 表1:48V 分散式架構與高密度電源模組相結合,將使精巧型電動 SUV 減重約 18 公斤(40 磅)
這一點非常重要,因為美國聯邦公路管理局 2023 年的資料顯示,美國人平均每年開車的行駛里程為 14,263 英里。因此,使用 48V 分散式架構可減少每年 30% 的充電時間(表 2),並增加車輛一次充電的行駛里程。 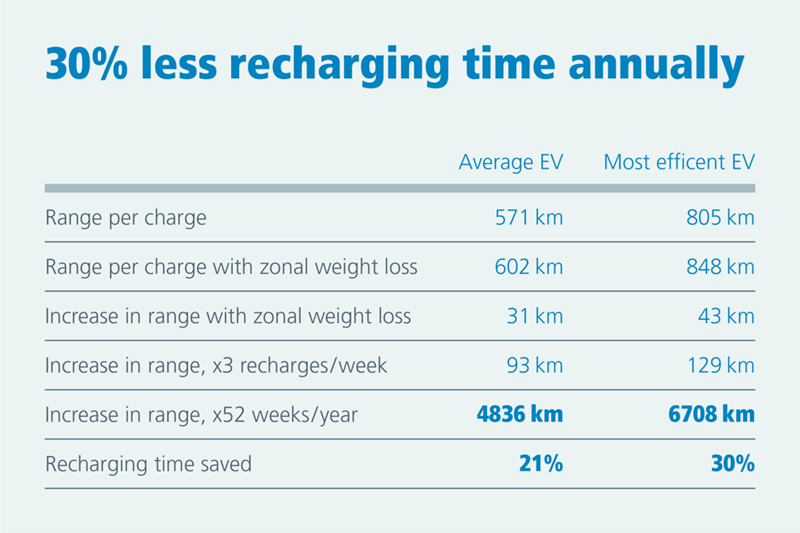 表2:增加的行駛里程為司機增加了每次充電的行駛距離,減少每年所需的充電次數。
以創新消除重量疑慮 電動汽車超重,這種趨勢既不能持續,也不利於電動汽車的整體發展。採用傳統銀盒和分立式元件的 12V 集中式架構需要升級到 48V 分散式架構,以最佳化電動汽車的供電網路和散熱管理系統。分散式架構可將每年的行駛里程增加 4000 英里,也可用於實現額外的安全或電子功能。 最高效的區域架構在負載點使用小型輕量級轉換器。高效的高功率密度模組是 48V 至 12V 轉換的最佳選擇。 鑒於目前複雜的汽車電力電子產品,OEM 廠商不僅需要創造性地減輕重量,同時還需要提高效能。Vicor 是高效能電源模組的領導者,始終致力於實現創新和創造。Vicor 精巧型電源模組、架構和拓撲為汽車 OEM 廠商提供高度靈活的可擴充電源解決方案,用於整個車輛的高壓電源轉換。易於部署的電源模組是原有集中式電源系統使用的傳統分立式設計的替代方案。此外,小巧精巧的電源模組也是 48V 區域架構顯而易見的選擇及合理補充,48V 區域架構是汽車產業供電網路的未來。
|